What is the specific operation process to extend the service life of insulating paint?
Published on:
2024-10-08
Specific operation process to extend the service life of insulating paint
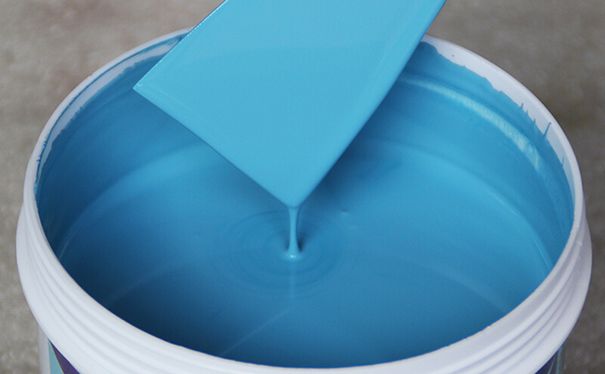
-
Work environment improvement operation process
- Temperature control
- Pre-Installation Assessment: Before installing electrical equipment, first determine the heat generated by the equipment during normal operation, and select the appropriate heat dissipation method according to the heat resistance level of the insulating paint and the heating condition of the equipment. For example, for a high-power motor, look at the power loss parameter in its specification to estimate heating.
- Heat sink installation:
- Cooling Fan-Installation: If you choose to install a cooling fan, first determine the size and number of fans according to the space and cooling requirements of the device. During installation, ensure that the direction of the air outlet of the fan is correct, and the hot air can be effectively discharged from the outside of the equipment. For example, on a computer CPU radiator, install a fan on one side of the radiator fins to make the wind blow to the fin gap to take away heat.
- Radiator Installation: For some equipment that needs to dissipate heat through conduction, such as the power tube in the power amplifier, choose a suitable radiator (such as aluminum radiator). In the installation process, to use thermal grease to ensure good heat conduction between the power tube and the radiator. Apply the thermal grease evenly on the heat dissipation surface of the power tube, then fit the radiator closely on it and fix it with screws.
- Operation monitoring and adjustment: After the equipment is put into operation, use temperature sensors (such as thermocouples or thermistors) to monitor the temperature of key parts of the equipment. If the temperature is found to be too high, check whether the heat dissipation device is working normally, such as whether the cooling fan is rotating, whether the radiator is blocked, etc., and make adjustments or repairs in time.
- Humidity regulation
- Environmental Assessment: Assess the humidity of the environment where the equipment is located, and formulate corresponding moisture-proof strategies for environments where the humidity often exceeds the suitable range of insulating paint (generally 40%-60%), such as basements and coastal areas.
- Implementation of moisture-proof measures:
- Desiccant placement: If it is a small device, such as a power distribution box, an appropriate amount of desiccant (such as silica gel desiccant) can be placed inside the device. Put the desiccant in a bag or container with good air permeability, place it at the corner or bottom of the equipment, check the status of the desiccant regularly, and replace it in time when the color change of the desiccant indicates that the water absorption is saturated.
- Installation of dehumidification equipment: For larger spaces or environments with strict humidity requirements, such as electronic equipment production workshops, install industrial dehumidifiers. According to the workshop area and space height, select the appropriate amount of dehumidification dehumidifier. After installation, set the appropriate humidity control parameters to keep the humidity in the workshop within the ideal range.
- Sealing treatment: For equipment that needs to be waterproof, such as outdoor motors, use sealant at the interface of the equipment's shell for sealing. When applying the sealant, ensure that the interface is clean and dry, and the sealant is evenly applied without bubbles and gaps to prevent moisture from penetrating.
- Protection against chemical substances
- environmental analysis: Analyze chemical corrosive substances that may exist around the equipment, such as in a chemical workshop, to determine which acids, alkalis, organic solvents and other substances may come into contact with electrical equipment.
- Protective measures taken:
- Enclosure protection: If possible, choose corrosion-resistant housing materials, such as stainless steel, plastic (chemical-resistant varieties), etc. When installing the housing, ensure the sealing of the housing to prevent chemical substances from entering the gap.
- Coating protection: Apply a layer of anti-corrosion paint on the outer layer of insulating paint. First of all, choose the anti-corrosion coating compatible with the insulating paint. Before coating, clean and pre-treat the surface of the equipment (such as polishing, degreasing, etc.), and then uniformly coat according to the instructions for the use of the coating. It usually needs to be coated with multiple layers, with sufficient drying time between each layer.
- Temperature control
-
Electrical parameter control operation process
- Voltage Management
- Determination of operating voltage: In the equipment installation and debugging stage, accurately measure the voltage range of the equipment during normal operation, and set reasonable voltage protection parameters according to the rated voltage and actual working conditions of the equipment.
- Installation of voltage regulation and protection devices:
- Voltage Regulator Installation: For equipment that requires stable voltage, such as precision electronic equipment, install automatic voltage regulators. During the installation process, correctly connect the input and output lines according to the wiring diagram of the equipment to ensure that the rated power of the regulator can meet the power requirements of the equipment. After the installation is completed, debug and check whether the output voltage is within the set range.
- Surge protector installation: For equipment that is susceptible to lightning strikes or may have surge voltage, such as outdoor power transformers, install surge protectors. Select the appropriate specifications of the surge protector, its rated voltage and current capacity to meet the electrical parameters of the equipment requirements. Install the surge protector at the power input of the equipment and connect the wiring in the correct wiring method to ensure that the current can be effectively guided to the ground when the surge voltage occurs.
- current frequency control
- Equipment design stage: When designing high-frequency electrical equipment (such as high-frequency transformers), select appropriate winding materials (such as Litz wire) and core materials (such as ferrite) according to the operating frequency and performance requirements of the equipment. By optimizing the number of turns, wire diameter and arrangement of the winding, the loss caused by high frequency current is reduced.
- Operation phase monitoring and adjustmentDuring the operation of the equipment, use professional instruments (such as spectrum analyzer) to monitor the current frequency and the loss of the equipment. If abnormal frequency or excessive loss is found, check whether the components in the circuit are damaged or whether the parameters have changed, such as whether the values of capacitance and inductance have changed, and adjust or replace them in time.
- Voltage Management
-
Mechanical damage prevention operation process
- Protection against vibration and shock
- Equipment pre-installation planning: Before installing the equipment, evaluate the vibration source and possible impact in the operating environment of the equipment. For equipment that is easily affected by vibration, such as on-board electronic equipment, choose the appropriate installation location and shock absorption method.
- Installation of damping device:
- Installation of shock pad: If you choose to install a shock-absorbing pad, select the appropriate shock-absorbing pad model (such as rubber shock-absorbing pad) according to the weight and vibration frequency of the equipment. Place the shock pad on the bottom of the device, ensuring that the device is completely isolated from the installation plane by the shock pad. For example, in the installation of an outdoor unit of an air conditioner, rubber shock absorbers are placed under the four corners of the outdoor unit to reduce the transmission of vibration during operation of the outdoor unit to the building.
- Construction of damping platform: For large industrial motors and other equipment, build a shock-absorbing foundation platform. The platform can be built using a combination of spring shock absorbers or rubber shock absorbers. In the construction process, to ensure the flatness and stability of the platform, the motor is installed on the platform, so that the vibration of the motor is effectively absorbed by the damping device of the platform.
- Transport protection measures: During the transportation of the equipment, choose the appropriate packaging material according to the size, weight and fragility of the equipment. For small precision equipment, use foam plastic, air cushion film and other cushioning materials for multi-layer packaging. For large equipment, in addition to the use of cushioning materials, but also the use of wooden boxes or iron boxes and other packaging for reinforcement, in the box marked "fragile", "handle with care" and other signs.
- Avoid wear
- Equipment Design Phase Considerations: When designing equipment, for places with relatively moving parts, such as the shaft and bearings of the motor, ensure that there is sufficient clearance to avoid friction between the parts. According to the shaft diameter and speed and other parameters, calculate the reasonable gap size.
- Wear-resistant materials and lubricants used: Use wear-resistant materials to isolate the parts where friction may occur. For example, wear-resistant bushings are mounted at the journals of the motor. At the same time, use a suitable lubricant, such as grease or lubricating oil. When adding lubricant, it should be added in accordance with the requirements of the equipment to avoid too much or too little lubricant. For some equipment that needs long-term operation, check and supplement the lubricant regularly.
- Protection against vibration and shock

Zhaoqing Ruixin Chemical Technology Co.Ltd
Address: No.7, Chuangzhan 3rd Street, Jianggu Fine Chemical Park, Sihui City, Guangdong Province, China
Whatsapp: +8618676585274